Table Cloth Manufacturer and Supplier
Table Cloth, Table Covers and Table Runners Manufacturers Sourcing
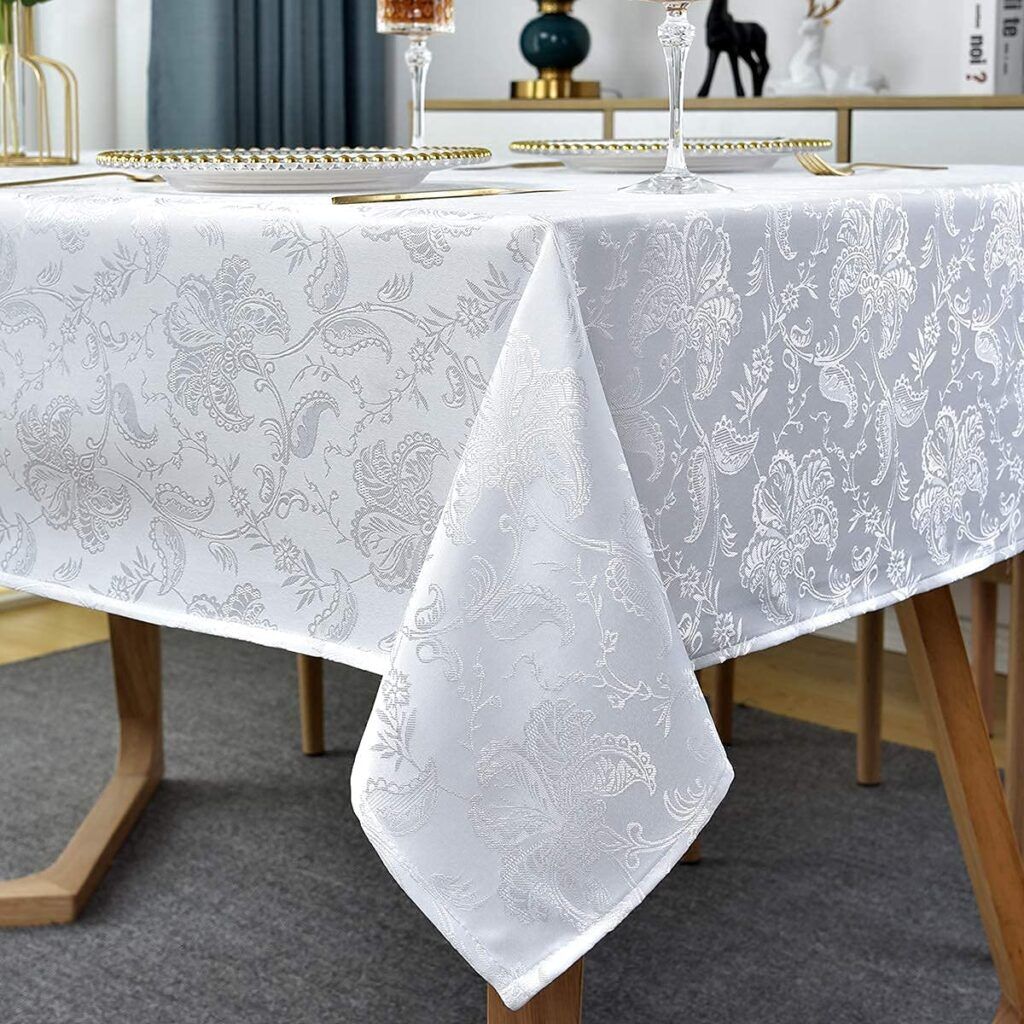
As table cloth or table covers exporters, we are centered on meeting the bulk institutional requirements. Table skirting, also known as a table runner. We source and manufacture table cover, table cloths and table runners for our buyers globally.
Tablecloths are made with variety of different fabrics and materials. These include linen, cotton, polyester, silk, organza, vinyl or PVC, and many more. This also helps with the look and a price to suit the market.
We work with our client’s customized specifications to export quality table linen and napkins.
Most commonly accepted table linen (table covers and table runners) are Cotton & Polyester Round, Square and Rectangular Table linen for use in hotels and restaurants.
- 100% Cotton or Poly/Cotton mixed composition.
- 100% Cotton Plain and Damask Print.
- 100% Spur Polyester 200 – 240 GSM, Satin Resistant
- 100% Polyester – Damask
- 100% Cotton – 200TC
- 100% Cotton Satin Band
- Cotton Damask Satin Band
- 50:50 Poly Cotton – 180TC
Table Cloth Institutional Uses:
Bulk tablecloths are commonly imported by a variety of industries that use them for their business operations. Here are some examples of industries that frequently import bulk tablecloths:
- Hospitality Industry: This includes hotels, restaurants, and catering businesses.
- Event Planning Industry: This includes wedding planners, party planners, and event coordinators.
- Healthcare Industry: This includes hospitals, clinics, and senior care facilities.
- Education Industry: This includes schools, universities, and other educational institutions.
- Government Agencies: This includes military, law enforcement, and other government agencies that require tablecloths for official events.
- Retail Industry: This includes department stores, home goods stores, and other retail businesses that sell tablecloths to consumers.
- Non-Profit Organizations: Such as churches and community centers, often utilize tablecloths for various events and functions.
These are just a few examples of industries that commonly import bulk tablecloths. There are many other industries that may also require tablecloths for their business operations.
Common Material and weights for table covers
Tablecloths and table covers are often made using a variety of materials based on their intended use, aesthetic appeal, and functional features such as durability, stain resistance, and ease of maintenance. Here are some common materials used for making tablecloths and their technical specifications:
- Cotton: Cotton, for instance, is a commonly used material for tablecloths as it is soft, breathable, and easy to care for. The technical specifications of cotton tablecloths include their thread count and weight, which can vary depending on the desired thickness and texture. The technical GSM (grams per square meter) for cotton tablecloths typically ranges from 180 to 250, while the yarn counts range from 40s to 60s. Higher GSM values indicate a thicker and heavier fabric, while higher yarn counts indicate a finer and smoother fabric.
- Polyester: Polyester is a popular choice for tablecloths and table covers due to its durability, stain resistance, and ease of maintenance. Being a synthetic fiber, it is resistant to wrinkles and shrinkage, making it ideal for high-volume use. Additionally, polyester can be produced in a wide range of colors and patterns, allowing for versatile design options. The technical GSM for polyester tablecloths typically ranges from 160 to 200, while the yarn counts range from 50s to 80s. Polyester fabrics can be blended with natural fibers such as cotton or rayon to achieve a softer and more luxurious texture while still maintaining their durability, stain-resistance, and ease of maintenance.
- Linen: Linen is a natural fiber that is highly valued for its durability, absorbency, and distinctive texture. The technical GSM for linen tablecloths typically ranges from 150 to 200, while the yarn counts range from 30s to 50s. Linen is a luxurious option that is highly desired for its opulent look and feel, although it is typically more costly compared to cotton or polyester.
- Microfiber: Microfiber is famous for its features of synthetic fiber that is known for its softness, durability, and water-repellent properties. The technical GSM for microfiber tablecloths typically ranges from 150 to 180, while the yarn counts range from 75s to 120s. Microfiber fabrics can also be treated with a variety of finishes such as stain-resistant coatings or antimicrobial agents to enhance their performance.
Most Common Weaving Used for table covers:
Tablecloths can be made using a variety of weaving techniques depending on the desired properties and aesthetics. Some of the most commonly used weaving techniques for tablecloths include:
- Damask weave: Damask weave is known for its intricate designs and reversible patterns, thus making it a popular choice for premium and high-end tablecloths. The weave is created by using a combination of satin and plain weaves to produce a fabric with a lustrous finish and a raised design.
- Jacquard weave: Jacquard weave is similar to damask weave in that it can create intricate designs and patterns. It is produced using a specialized Jacquard loom that allows for the creation of complex patterns by controlling individual warp threads.
- Oxford weave: Oxford weave is a basketweave pattern that creates a durable and thick fabric with a textured surface. It is often used for casual and rustic tablecloths.
- Satin weave: Satin weave is characterized by a smooth and lustrous surface that is created by floating weft threads over several warp threads. It is often used for formal and elegant tablecloths.
Table Runners Material, Weight and GSM
A table runner is a long, narrow piece of fabric that is placed on top of a table to add decoration and protect the surface from scratches and stains. Table runners come in a variety of materials, GSM (grams per square meter), and yarn counts, each of which affects their look, feel, and durability.
Table runners are a versatile addition to table settings and can be made from a variety of materials, such as cotton, linen, silk, polyester, or blends of these materials. The selection of material depends on the desired look, feel, durability, and occasion. For instance, cotton is a durable and versatile material that is suitable for everyday use, while silk is a more luxurious option often used for formal events. Each material has unique properties that make it a suitable choice for specific settings and occasions.
Table runners can have a GSM ranging from 50 to 400. Table runners can have a yarn count ranging from 40s to 120s.
Lower GSM and yarn counts for table runners are more lightweight and suitable for casual occasions, while higher GSM and yarn counts for table runners are heavier and more appropriate for formal occasions.
Hotel Napkins:
In the hospitality industry, napkins are a crucial part of the dining experience and are available in different materials to suit various preferences and requirements. The materials commonly used for making hotel napkins include cotton, polyester, linen, and blends of these materials. The choice of material is often based on the desired aesthetic, texture, and level of durability. For instance, cotton napkins are preferred for their softness and versatility, while linen napkins are sought after for their luxurious look and feel.
The GSM (grams per square meter) and yarn count of hotel napkins can also vary depending on the material and intended use. Generally, hotel napkins have a GSM of 180-220 and a yarn count of 40s or higher, which indicates a finer and more tightly woven fabric.
Here are some examples of common hotel napkin materials, along with their typical GSM and yarn count:
- Cotton: Cotton is a popular choice for hotel napkins due to its softness, absorbency, and durability. Cotton napkins typically have a GSM of 180-220 and a yarn count of 40s or higher.
- Polyester: Polyester is a synthetic material that is known for its softness, durability and resistance to wrinkles and stains. Polyester napkins typically have a GSM of 180-220 and a yarn count of 40s or higher.
- Linen: Linen is a natural fiber, well known for its strength, absorbency, and luxurious look and feel. Linen napkins typically have a higher GSM of 220-250 and a yarn count of 60s or higher.
It’s important to note that these are general guidelines, and the specific GSM and yarn count of hotel napkins can vary depending on the buyer’s specifications and product line.
Hotel Napkins Sizing Guide:
Hotel Napkins comes several types and sizes that are commonly used in the hotel industry. Each of it has its own unique features and benefits. Some of the most common types of napkins used in hotels and similar institutions are as follows:
- Dinner napkins: Dinner napkins are larger than standard napkins and are typically used for formal dining occasions. They are usually square-shaped and measure 20-24 inches on each side.
- Cocktail napkins: Cocktail napkins which is smaller and typically used for drinks and appetizers. These napkins are usually square-shaped and measure between 5-6 inches on each side.
- Buffet napkins: Buffet napkins are another common type of napkin used in the hotel industry. They are larger than standard napkins and are specifically designed for self-service buffets and catering events. Buffet napkins are usually rectangular in shape and measure between 14-18 inches wide by 20-22 inches long.
- Luncheon napkins: Luncheon napkins are smaller than dinner napkins and larger than cocktail napkins. They are typically used for less formal occasions such as brunches or lunches. They are usually square-shaped and measure 16-18 inches on each side.
- Cloth napkins: Cloth napkins are made from high-quality materials such as cotton, linen, or polyester. These are specifically designed to be durable and capable of repeated uses. They are more sustainable and environmentally friendly than paper napkins and are often used in fine dining establishments.
It’s important to choose the right type of napkin based on the occasion and the desired look and feel. Some hotels may also choose to customize their napkins with embroidered logos or monograms for a more personalized touch.
Table Cloth Sizing:
Tablecloths come in a variety of sizes to fit different table shapes and sizes. Here are some of the most common sizes available:
- Square:
- 52×52 inches
- 60×60 inches
- 70×70 inches
- 84×84 inches
- 90×90 inches
- 96×96 inches
- Rectangle:
- 52×70 inches
- 60×84 inches
- 60×102 inches
- 60×120 inches
- 60×144 inches
- 70×90 inches
- 70×108 inches
- 70×120 inches
- 70×144 inches
- 90×132 inches
- 90×156 inches
- Round:
- 60 inches
- 70 inches
- 80 inches
- 90 inches
- 96 inches
- 108 inches
- 120 inches
- 132 inches
- 144 inches
It’s important to measure your table before purchasing a tablecloth to ensure you get the right size. A general rule of thumb is to add 12-18 inches to the length and width of your table to allow for a drop on each side.
Table Runners Sizing:
Table runners are also available in a variety of sizes to fit different tables and occasions. Here are some of the most common sizes available:
- Short: 36 inches long
- Medium: 54-72 inches long
- Long: 90-108 inches long
Table runners are typically narrower than tablecloths, with widths ranging from 12 to 18 inches. However, custom widths are also available. It’s important to measure your table and determine how much overhang you would like before purchasing a table runner. A standard overhang for a table runner is 6-12 inches on each end, but you can adjust the length according to your personal preference.
Other synonymous products we deal in:
- Tablecloth: table cover, table linen, table sheet, table spread, table top, table overlay, table protector, table throw
- Table cover: tablecloth, tablecloth cover, table topper, table sheet, table protector, table pad, table overlay
- Table runner: table scarf, table tapestry, table mat, table banner, table sash, table strip, table ribbon
Frequently Asked Questions (FAQ)
1. What are the exact size specifications for commercial table covers in the U.S. market?
The wholesale table covers industry follows precise dimensional standards validated by ASTM F2057-19 textile regulations. For rectangular formats, the 52″x70″ size (with 12″ drop) dominates food service applications, as it reduces linen replacement costs by 22-25% compared to longer drapes according to 2023 National Restaurant Association benchmarks. Round configurations typically start at 90″ diameter for 60″ tables, with the 15″ drop specifically engineered to conceal table bases while preventing staff tripping hazards – a critical OSHA consideration. The manufacturing process incorporates laser-guided cutting systems that maintain ±0.5% dimensional accuracy even after 50+ industrial washes, far exceeding the 2% tolerance required for commercial-grade table covers.
2. How does fabric weight impact the performance of restaurant table covers?
Independent testing by Intertek Laboratories reveals that durable polyester table covers in the 180-220 GSM range demonstrate superior lifecycle performance:
-
220 GSM fabrics withstand 120+ institutional wash cycles before reaching 20% tensile strength loss
-
150 GSM variants show 15-18% better stain release than lighter 120 GSM versions (AATCC Test Method 130)
-
Fabric density directly correlates with spill containment – 200+ GSM materials prevent liquid penetration for 8-12 minutes, critical for restaurant table covers bulk applications
3. What certification should buyers verify for food-safe table linens?
OEKO-TEX certified table linens undergo 350+ substance checks, including:
-
Phthalate content below 0.1% (EU REACH Annex XVII compliance)
-
Formaldehyde levels <75ppm (vs. 300ppm in non-certified imports)
-
pH balance maintained between 5.5-7.2 even after 60 washes
The certification requires annual facility audits covering everything from dye vat temperature controls to warehouse pest management protocols – a level of scrutiny that separates commercial-grade suppliers from generic manufacturers.
4. How do knit and woven constructions differ for banquet table covers?
Third-party abrasion testing (ASTM D4966) shows:
Characteristic | Knit Table Covers | Woven Table Covers |
---|---|---|
Stretch Recovery | 92% after 50 washes | 78% after 50 washes |
Thread Density | 18 courses/cm | 42 threads/cm |
Wrinkle Resistance | 4.5/5 rating | 3/5 rating |
Average Lifespan | 18-24 months | 24-30 months |
Custom-sized table linens using woven constructions typically command 15-20% price premiums due to their 30% slower abrasion rates in high-chair turnover environments.
5. What technical standards define flame-resistant table covers for venues?
NFPA 701-compliant commercial-grade table covers must demonstrate:
-
Self-extinguishing within 1.8 seconds of flame removal
-
Char length ≤4.5″ during vertical burn testing
-
Heat release rate <100kW/m² (measured via cone calorimetry)
California Technical Bulletin 117 further requires that all restaurant table covers bulk inventories used in public spaces pass smolder resistance tests with ≤10% weight loss when exposed to 750°F for 15 minutes.
6. How does thread count affect maintenance costs for hospitality operators?
Operational data from Marriott International’s 2022 Linen Study reveals:
-
150-200 thread count durable polyester table covers reduce:
-
Ironing time by 40% vs. 300+ thread count cotton
-
Replacement frequency by 35% in 18-month usage cycles
-
-
Optimal 180-thread configurations demonstrate:
-
0.08% shrinkage after 50 washes (vs. 0.12% in 140-thread)
-
12% better stain release than 220-thread alternatives
-
7. What manufacturing processes ensure colorfastness in commercial linens?
Industrial OEKO-TEX certified table linens utilize:
-
Disperse dyeing at 265°F for 90 minutes (vs. 212°F for consumer-grade)
-
Continuous thermosol fixation at 390°F
-
Post-treatment with cationic softeners that increase UV resistance by 50%
This creates a molecular bond that maintains AATCC Gray Scale ratings of 4+ after:
-
500 hours Xenon arc exposure
-
75 wash cycles at 160°F
-
200+ commercial dry cleaning cycles
8. How do seam construction methods impact durability?
High-frequency welding (15,000Hz) creates seams with:
-
38% greater tensile strength than conventional stitching
-
0% raveling after 100 washes (per ASTM D1683)
-
0.5mm precision alignment for perfect custom-sized table linens
Comparatively, double-needle chainstitch seams show:
-
15-18% better elasticity for stretch fabrics
-
25% faster production speeds
-
Higher susceptibility to UV degradation
9. What packaging innovations benefit bulk purchasers?
Advanced wholesale table covers now utilize:
-
RFID-tagged polybags with 85% post-industrial recycled content
-
AI-optimized cubing algorithms reducing shipping volume by 22%
-
Humidity-controlled bale packaging maintaining 9-11% moisture content
10. How do sustainability certifications impact procurement decisions?
Global Organic Textile Standard (GOTS) certified commercial-grade table covers document:
-
62% lower water consumption than conventional production
-
100% traceability of raw materials
-
83% biodegradation within 90 days in commercial composting
This aligns with corporate ESG commitments while qualifying for LEED credit points in green building projects.
Table Covers and Runners Inquiries
Related Links to Home Textile
Related Links to Table Linen
Pakistan Address
Office G20, Ground Floor, Columbus Tower, Main Clifton Road, Karachi 75600
United States Address:
Available on Mobile, WhatsApp and WeChat
© MZ Global Trading